Precision Industrial Refractometers for Coolant Management
Accurately monitor and optimize coolant concentration for better machining performance and cost savings.
View Our Refractometers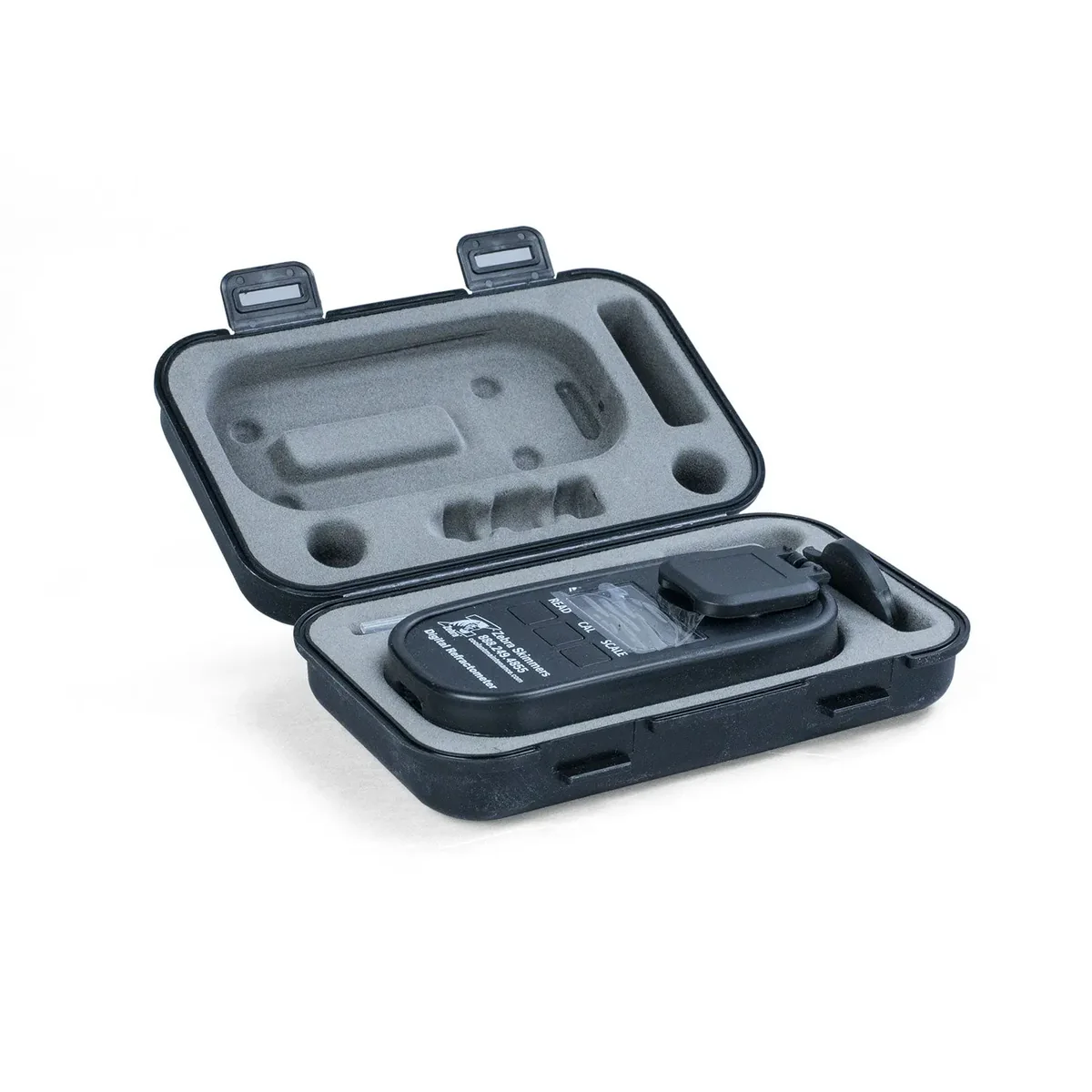
✓ Accurate Measurements
Precise Brix and concentration readings for optimal coolant performance.
✓ Cost Effective
Reduce waste and extend tool life with proper coolant management.
✓ Easy to Use
Quick, reliable measurements without specialized training.
Trusted by manufacturers worldwide
Why Your Shop Needs a Quality Refractometer
Maintaining proper coolant concentration is critical for optimal CNC machining performance. Industrial refractometers provide fast, accurate measurements that help you:
✓ Extend Tool Life
Proper coolant concentration reduces tool wear and extends tool life by up to 30%.
✓ Improve Surface Finish
Consistent coolant mixture ensures better surface quality on machined parts.
✓ Reduce Coolant Costs
Prevent waste by maintaining optimal concentration levels and reducing disposal costs.
✓ Prevent Downtime
Avoid machine damage and production delays with proper coolant management.
Choose the Right Refractometer for Your Needs
Zebra Skimmers offers a range of high-quality refractometers to meet your specific requirements.
Handheld Optical Refractometers
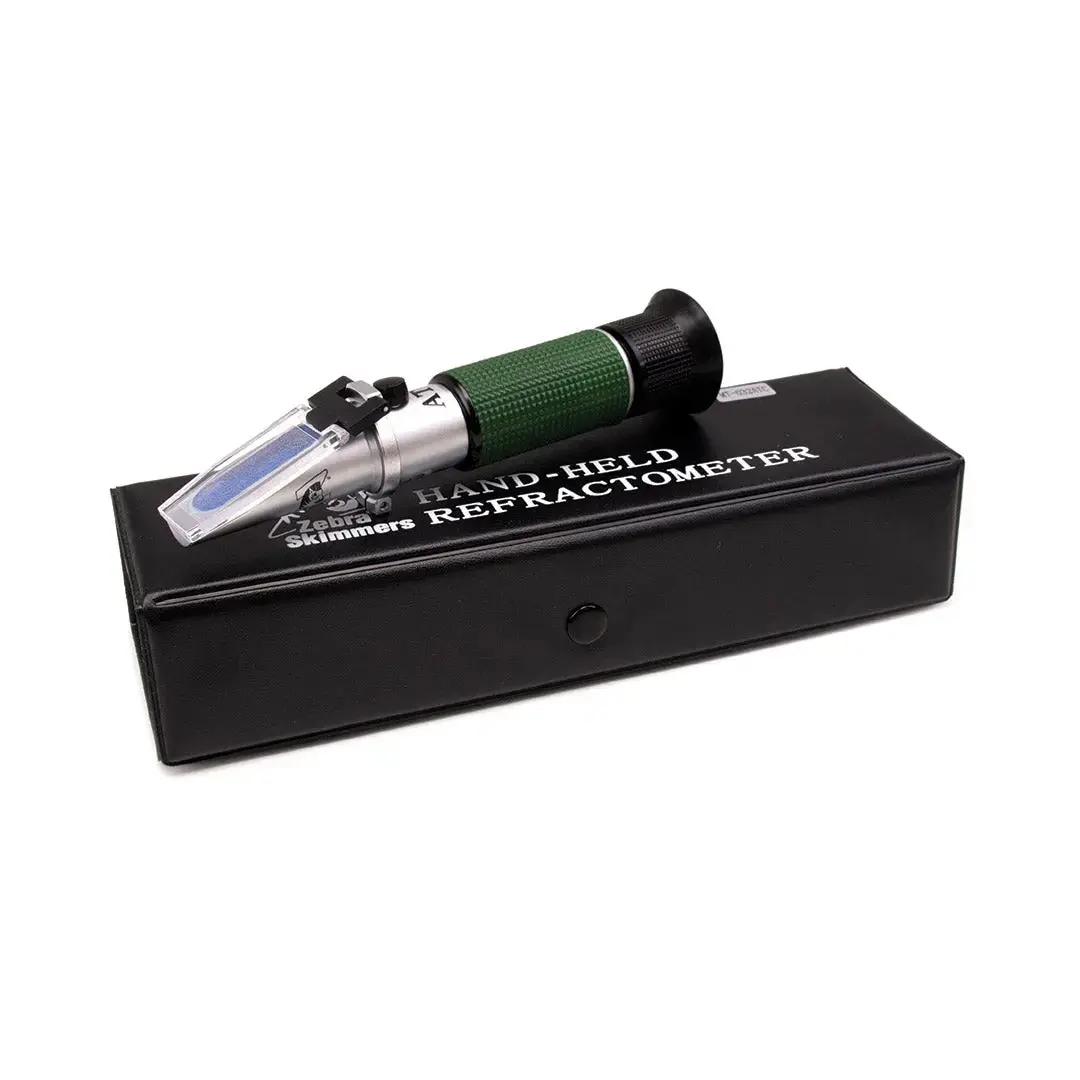
Standard Optical
Traditional handheld refractometer with clear scale for accurate Brix readings.
View Product →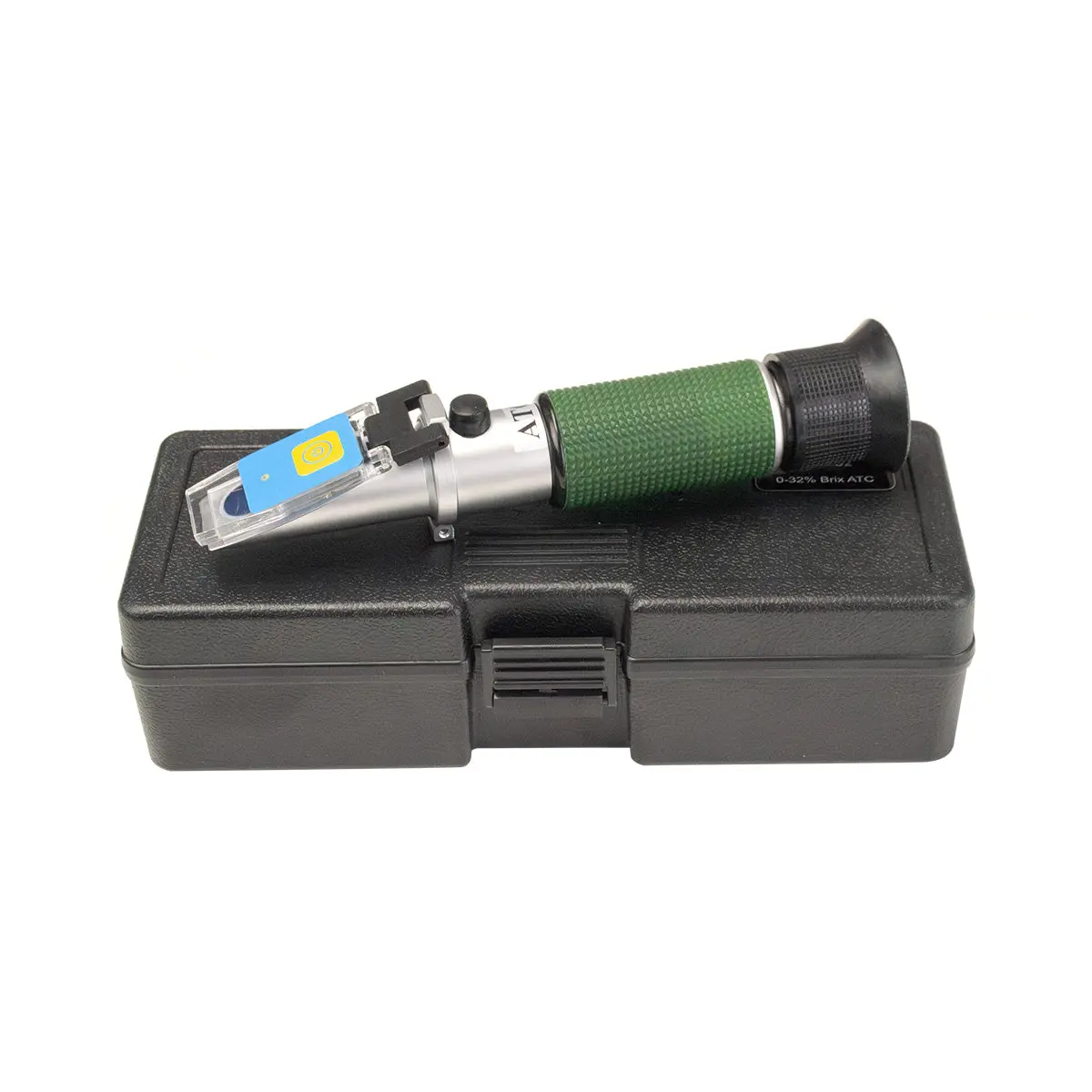
With LED Light Source
Enhanced visibility with built-in LED light for better readings in low-light conditions.
View Product →Digital Refractometers
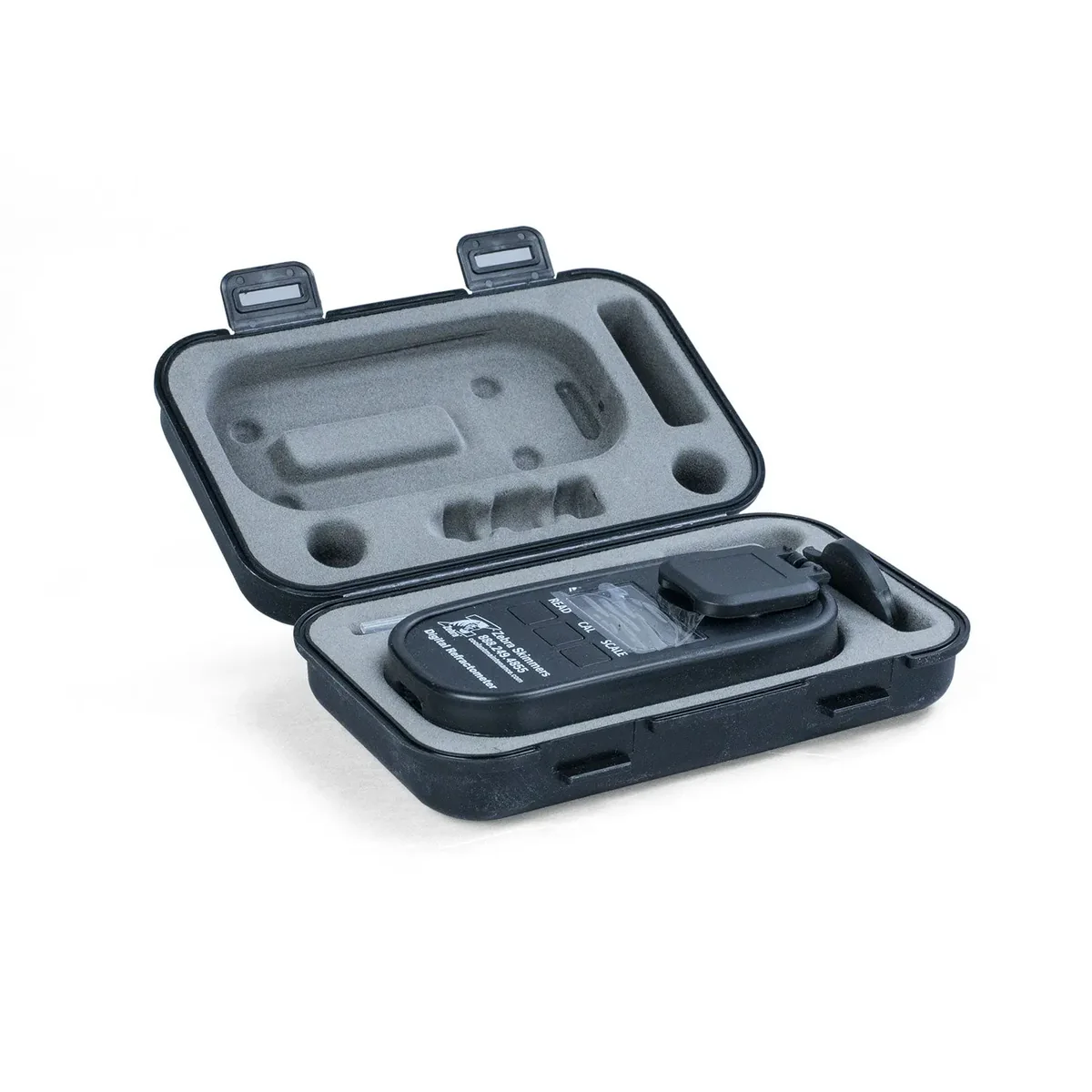
Digital Precision
Advanced digital refractometer with LCD display for precise readings without interpretation errors.
View Product →Refractometer Sump Maintenance Kits
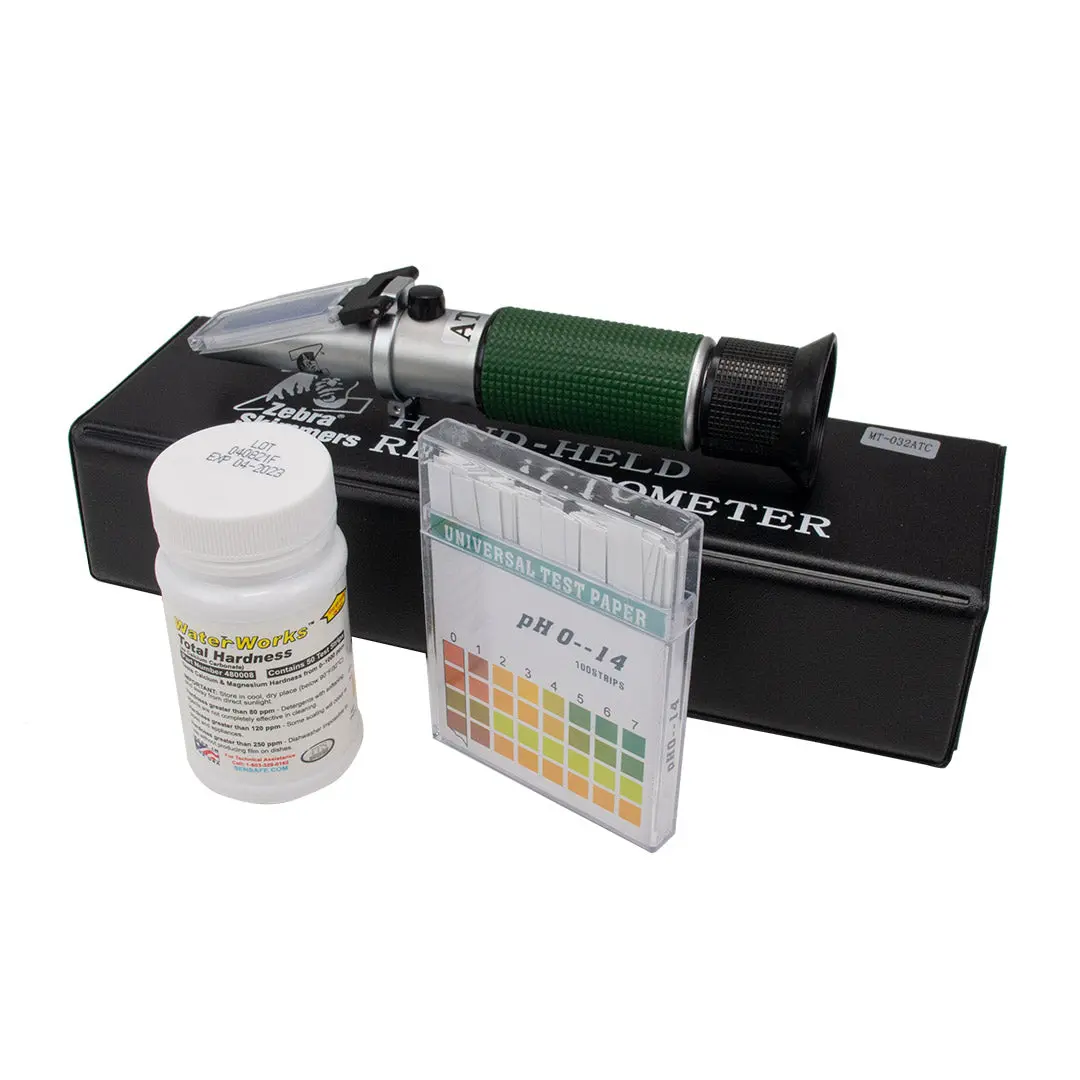
Standard Kit
Complete kit for effective coolant maintenance including refractometer and essential tools.
View Product →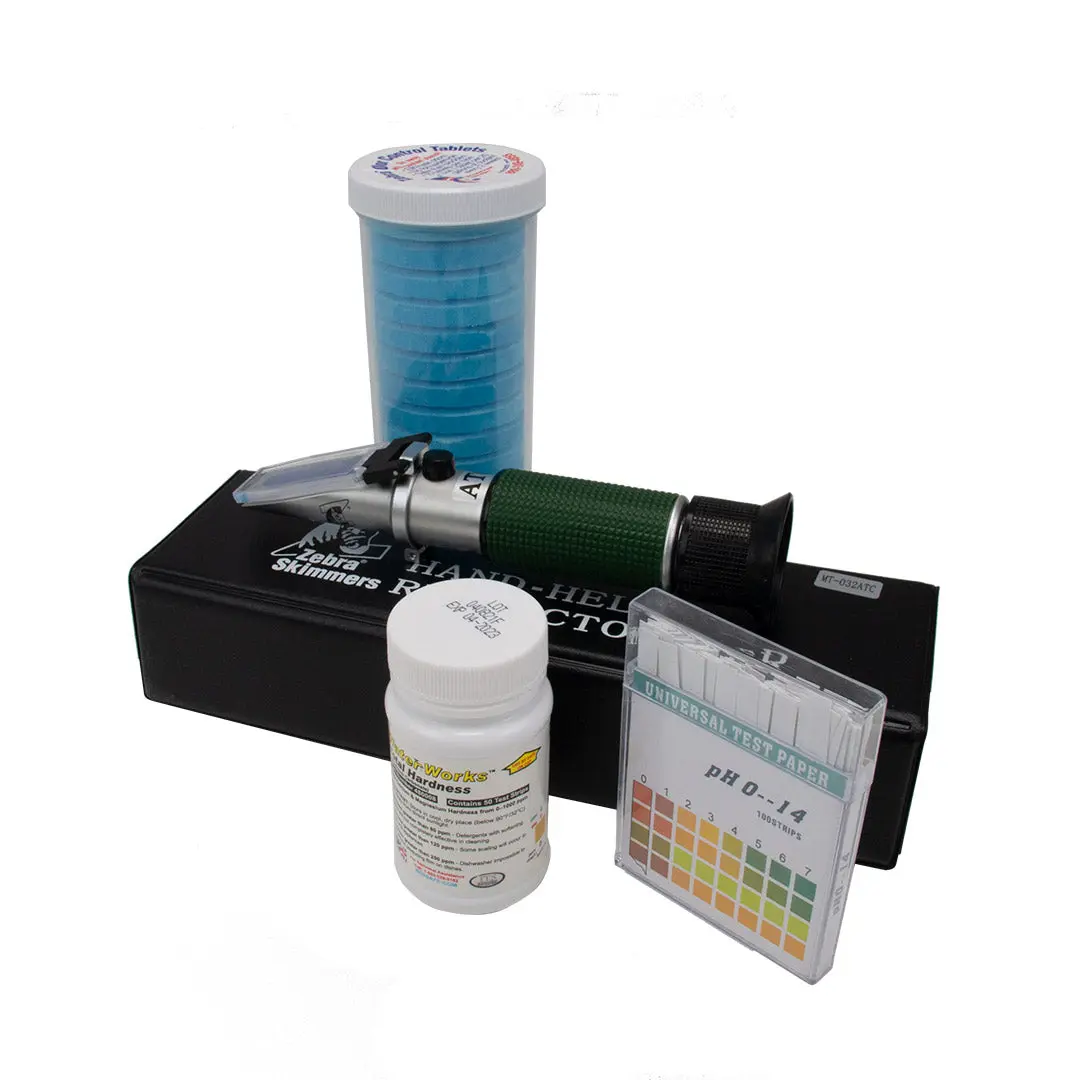
Plus Kit
Enhanced maintenance kit with additional tools for comprehensive coolant system management.
View Product →Understanding Refractometer Correction Factors
Keeping coolant concentration on-spec is one of the quickest ways to extend tool life, fend off rust and odor-causing microbes, and keep foaming under control. Because each coolant chemistry bends light a little differently, the raw °Bx (Brix) number you see on a handheld refractometer is only half the story.
Why a correction factor is needed
When white (emulsion), semi-synthetic, or fully synthetic fluids are blended, the oils, esters, and additives change the solution's refractive index. Two coolants that both look like 5% by volume on a refractometer scale can be radically different in reality—unless you compensate with the right multiplier, typically ranging from 1.0 for "direct-read" products up to about 2.2 for heavy-duty soluble oils.
Step-by-step: applying the factor
- Zero the refractometer with distilled water.
- Collect a representative sample—mid-sump, away from tramp oil, immediately after a few minutes of circulation.
- Place 1–2 drops on the prism, close the cover, and read the °Bx value.
- Multiply °Bx × correction factor = true % concentration.
Typical correction factors
Coolant brand & grade | Factor | Notes |
---|---|---|
Castrol Hysol MB 50 | 1.1 | Light-duty, multi-metal emulsion |
Castrol Hysol T15 | 1.5 | General-purpose soluble oil |
Hysol 21 BF | 1.6 | High-lubricity emulsion |
TRIM SC520 | 1.8 | Low-foam synthetic |
Heavy soluble oil (example Tower MWF) | 2.2 | Extreme-pressure duty |
QualiChem Xtreme Cut 250C | 1.0 | "Direct-read" single-point factor |
Example 1 – Castrol Hysol T15 (factor 1.5)
- Target machine spec: 7%
- Refractometer reads 4.7 °Bx
- Calculation: 4.7 × 1.5 = 7.05% → right on target; no adjustment needed.
Example 2 – Synthetic with factor 1.8
- Maintenance guideline: keep between 6% and 8%
- Refractometer reads 3.5 °Bx
- 3.5 × 1.8 = 6.3% → at the low end; add concentrate until °Bx rises to ~4.0 (4 × 1.8 ≈ 7.2%).
Example 3 – Direct-read coolant (factor 1.0)
- Desired 9% sump concentration
- Reading: 9 °Bx
- No math needed; °Bx is already the % by volume.
Practical tips
- Keep a laminated cheat-sheet of factors at each machine.
- Re-check factor after switching batches—additive tweaks can shift the optical response slightly.
- Investigate sudden swings in refractometer readings; they often signal hard-water dilution, tramp-oil ingress, or bacterial breakdown rather than dosing errors.
Using correction factors consistently turns a simple pocket refractometer into a precision QA tool, tightening process control and saving both tools and coolant concentrate over the long haul.
Ideal for These Industrial Applications
Our refractometers are trusted by professionals across various industries for precise coolant and fluid measurement.
CNC Machining Centers
Maintain perfect coolant concentration for optimal tool performance and part quality in high-precision CNC operations.
View CNC Solutions →Metalworking & Fabrication
Ensure proper concentration of cutting fluids to extend tool life and improve surface finishes in all metalworking applications.
View Metalworking Solutions →Industrial Maintenance
Monitor and maintain coolant systems to prevent corrosion, bacterial growth, and costly equipment damage.
View Maintenance Tools →Ready to Improve Your Coolant Management?
Join thousands of manufacturers who trust Zebra Skimmers for their industrial refractometer needs.